CrimpCenter 64 SP
Fully Automatic Crimping Machine
Overview
The CrimpCenter 64 SP ensures highly efficient machine setup processes and provides you with a significant cost-per-lead advantage of 5 percent as well as 8 to 14 percent faster production compared to its predecessor. With the Dual ToolingShuttle quick-change system for example, you can prepare a new job while production is still running, change applicators and terminals in only 30 seconds and save more than one minute per operation compared to conventional changeover methods. And the CommandPod control device helps you to achieve fast and uncomplicated setup processes.
Furthermore, the CrimpCenter 64 Performance Package offers an extensive list of innovations: Application-specific default values for process parameters, automatic control of the pneumatic pressure of conveyor belts and gripper systems, a sophisticated straightening unit and a newly developed roller design for very thin, demanding cables. Add to this a deposit gripper system that ensures perfectly aligned production batches for easy removal. And with integrated crimp force monitoring for multiple stamped terminals as well as a split-cycle function, it is possible to process belted, preinsulated and even closed-barrel type terminals as standard.
- Dual ToolingShuttle terminal-feeding system
- Optimized default parameter settings
- Newly developed deposit gripper system
- Improved synchronization of the feeding unit and conveyor
- Optimized wire collection
- Improved straightening units
- Automatic pressure adjustment
Application Range
The CrimpCenter 64 SP processes wires with conductor cross sections from 0.13 to 6 mm² and features the latest quality assurance options such as SmartDetect, WireCam 2.0 and the Guided Feasibility Study. These features qualify the CrimpCenter 64 SP as a first-class machine for complex and high-precision production with high quality requirements. In addition, the sophisticated network technology allows the integration of numerous quality assurance options, ensuring transparency and traceability of important production data and relevant information.
Material
- Single Wire
Processing Capabilities
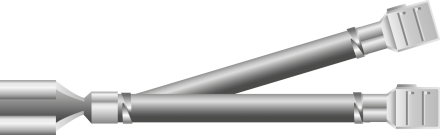


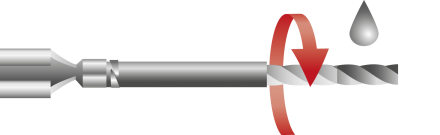

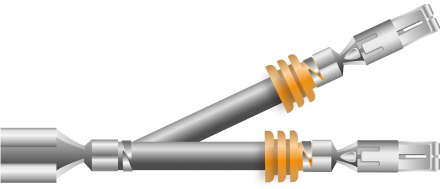


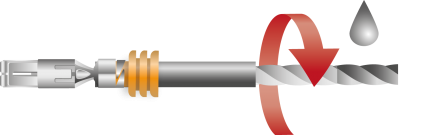
Technical Data
Processing Stations | Maximum 4 (maximum 2 crimping stations) |
Workpiece Length | 60 mm – 65 m (2.36“ – 213´) [optional from 35 mm (1.38“)] |
Strip Length | Side 1: 0.1 – 18 mm (0.004 – 0.71“) Side 2: 0.1 – 18 mm (0.004 – 0.71“) Optional cutter blocks for applications up to: Side 1: 26 mm (1.02“) and Side 2: 10 mm (0.39“) are available |
Conductor Cross Section | 0.13 – 6 mm² * (26 – 10 AWG) |
Raw Material Diameter | Maximum 6.3 mm (0.25“) |
Feed Rate | Maximum 12 m/s (39.37 ft/s) |
Power Supply | 3 / N / PE AC 210 500 V; 50 / 60 Hz; 16 A |
Compressed Air Connection | 6 bar (90psi), non-oiled, dried and filtered compressed air |
Dimensions (L x W x H) | 3,800 x 1,450 x approx. 1,860 mm (149“ x 57“ x 73“) / 2 m (6.5‘) base machine |
Height (Safety Cover Opened) | Approx. 2,900 mm (114“) |
Weight | Approx. 590 kg (1,300 lbs.) incl. base machine and safety cover |
CE Conformity | The CrimpCenter 64 SP complies with the CE and EMC equipment guidelines relative to mechanical and electrical safety as well as electromagnetic compatibility. |
Important Note | Schleuniger recommends that wire samples be submitted in cases where there is doubt as to the processing capabilities of a particular machine. |
More Info
Processing stations
- UniCrimp 221 crimping station with integrated crimp force monitoring (CFM 20)
- UniCrimp 222 crimping station with integrated crimp force monitoring (CFM 20) and electronic crimp height control
- SealLoad 3100 and SLU 3000 sealing stations
- SLD 4100 double gripper module
- STW 1100 twisting station
- STS 1100 tinning station
Options
- SmartDetect (including enhanced functionality)
- WireCam 2.0
- Material Change Detection (MCD)
- Guided Feasibility Study
- Two-wire straightener unit
- CAO / 4Wire Solutions
- Extension conveyors
- Integrated quality monitoring devices
- Prefeeding systems
- Barcode scanner
- Inkjet printer